Złamanie zmęczeniowe
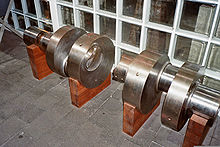

do Odlewane aluminium - korby rowerowej ;
światło: siła lub kruche pęknięcie

Na powierzchni pęknięcia widoczne są strefy pęknięcia: pozostawione pęknięcie, które istnieje od dłuższego czasu (ciemne); w kierunku środka obszar pęknięcia zmęczeniowego postępującego pod naprzemiennym obciążeniem z liniami stopu, od prawej kolejna strefa pęknięcia zmęczeniowego, pomiędzy wąską strefą pęknięcia wymuszonego
Jako pęknięcie zmęczeniowe , znane również jako pęknięcie zmęczeniowe lub potocznie jako pęknięcie trwałe lub zmęczeniowe , nazywane jest pęknięciem pod wpływem cyklicznego obciążenia. Większość pęknięć w inżynierii mechanicznej można przypisać pęknięciom zmęczeniowym. Zmęczenie elementu, na końcu którego następuje awaria lub pęknięcie elementu, zależy przede wszystkim od czasu trwania obciążenia i intensywności obciążenia spowodowanego zmiennym obciążeniem. Pęknięcie zmęczeniowe występuje wcześniej, im wyższa jest częstotliwość obciążenia zmiennego i im większa jest amplituda oscylacji. Poziom obciążenia można jakościowo wyprowadzić ze stosunku powierzchni pęknięcia zmęczeniowego do powierzchni pęknięcia siły resztkowej . Im większy obszar pęknięcia siły resztkowej, tym wyższe naprężenie nominalne działające na materiał.
W przeciwieństwie do wymuszonego zerwania, materiał jest poddawany naprężeniom wywołanym przez pęcznienie lub obciążenia oscylacyjne, które są poniżej granicy plastyczności , w zakresie sprężystym. Pod takimi przemiennymi obciążeniami można określić zmiany w mikrostrukturze materiału przy wystarczającej liczbie zmian obciążenia, które są oznaką zmęczenia materiału.
Linie łamliwe na powierzchni pęknięcia spowodowane przerywanym wzrostem pęknięcia są widoczną oznaką pęknięcia zmęczeniowego. Mikroskopijnym odpowiednikiem tego są bruzdy o bardzo drobnej strukturze, znane jako wibrujące paski. Zgodnie z teorią cykl zmiany obciążenia można wyznaczyć na podstawie odległości między dwoma drgającymi listwami, ale w praktyce jest to bardzo rzadko możliwe, ponieważ z. B. nie ma całkowicie równego obciążenia drganiami. Wibrujące paski są prawie pewnym wskaźnikiem cyklicznego naprężenia; nie należy jednak mylić z pęknięciem struktury perlitycznej . W większości przypadków linie blokujące i rodzaj przebiegu pęknięcia wystarczają do wykazania pęknięcia zmęczeniowego.
Działania, których należy unikać
Ponieważ przyczyną pęknięcia zmęczeniowego jest ostatecznie mechaniczne naprężenie przemienne, ważne jest, aby zmniejszyć to za pomocą środków konstrukcyjnych:
- Wystarcza wymiarowanie elementu dynamicznego stresu, na przykład przez wymiarowania przed awarią komponentu w najsłabszym punkcie przy pomocy Smitha lub Haigh diagramów , Wöhler linii diagramy lub przez zmęczenie lub obliczeń wytrzymałościowych obliczeń dynamicznych maszyna
- Unikanie dodatkowych naprężeń przemiennych z powodu drgań naturalnych
Naturalne drgania, które mogą być spowodowane przypadkiem obciążenia lub wzbudzeniem zewnętrznym, mogą być jedyną przyczyną uszkodzenia zmęczeniowego. Przykładem są wysokie, wytrzymałe, przewodowe elementy elektroniczne na płytkach drukowanych , które są stosowane na przykład w pojazdach silnikowych lub maszynach wibracyjnych lub błotniki i ich wsporniki w rowerach. W takich przypadkach sensowna jest zmiana częstotliwości drgań własnych układu wibracyjnego (najlepiej poprzez większą sztywność) lub tłumienie drgań. Okablowane, wystające elementy są więc często mocowane na płytkach drukowanych za pomocą kleju .
Oprócz wymiarowania elementu, ryzyko pęknięć zmęczeniowych w inżynierii mechanicznej jest zmniejszane różnymi środkami, których wspólnym celem jest uniknięcie punktu wyjścia do złamania. Takim punktem wyjścia jest tam, gdzie panuje duże napięcie lokalne , więc środki są przede wszystkim opłacalne w takich miejscach:
- Tworzenie zaokrąglonych przejść w przypadku zmian przekroju, unikanie nagłych zmian przekroju
- Unikanie nacięć, np. B. w wyniku
- Uszkodzić
- elementy konstrukcyjne takie jak gwinty i rowki
- specjalne cechy produkcyjne, takie jak nieprzetworzone szwy spawalnicze
- Twórz gładkie powierzchnie
- Wprowadzenie do powierzchni materiału ściskających naprężeń resztkowych , powszechne jest tu kulkowanie , które weryfikowalne naukowo wprowadza do materiału ściskające naprężenia resztkowe i wydłuża żywotność w przypadku obciążenia cyklicznego
- Obróbka przejść spoin metodą High Frequency Impact Treatment (w skrócie HiFIT) - proces wydłużania żywotności konstrukcji spawanych poprzez zaokrąglenie karbu geometrycznego, wygładzenie powierzchni, utwardzenie powierzchni oraz wprowadzenie naprężeń szczątkowych ściskających do głębokości 1,5 mm
- Unikanie wad produkcyjnych, takich jak powielanie i wtrącenia
- Użycie odpowiednich materiałów – zakłada się, że m.in. B. żeliwo z grafitem sferoidalnym w porównaniu z odlewem lamelarnym powoduje korzystniejszą krzywą naprężeń w mikrostrukturze
- Ochrona przed korozją, między innymi w celu uniknięcia pęknięć korozyjnych naprężeniowych
Indywidualne dowody
- ↑ zgodnie z wytyczną VDI 3822